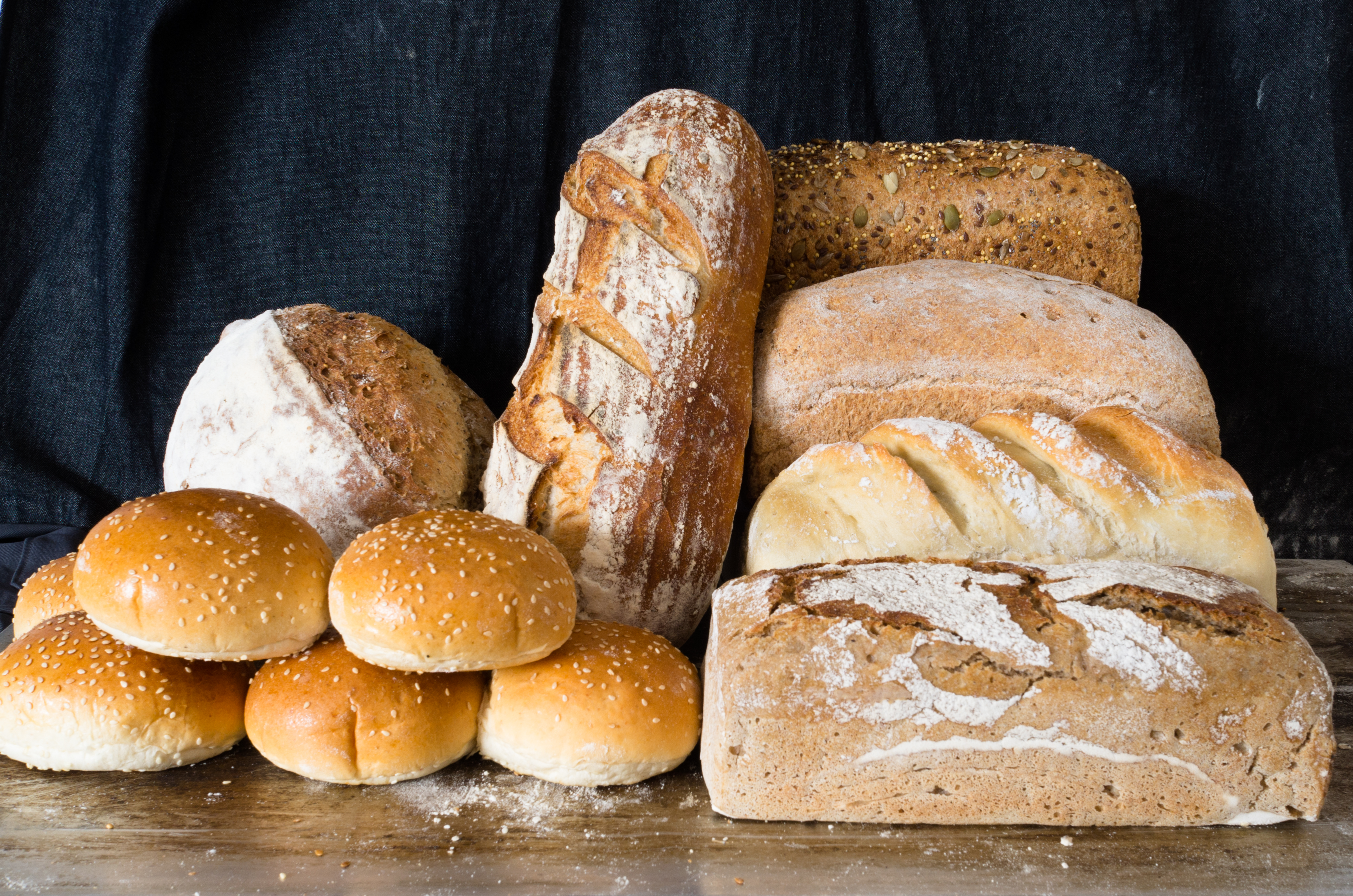
- Soil Association
- Certification
- Food & drink
- Certification Resources
- Inspection guidance
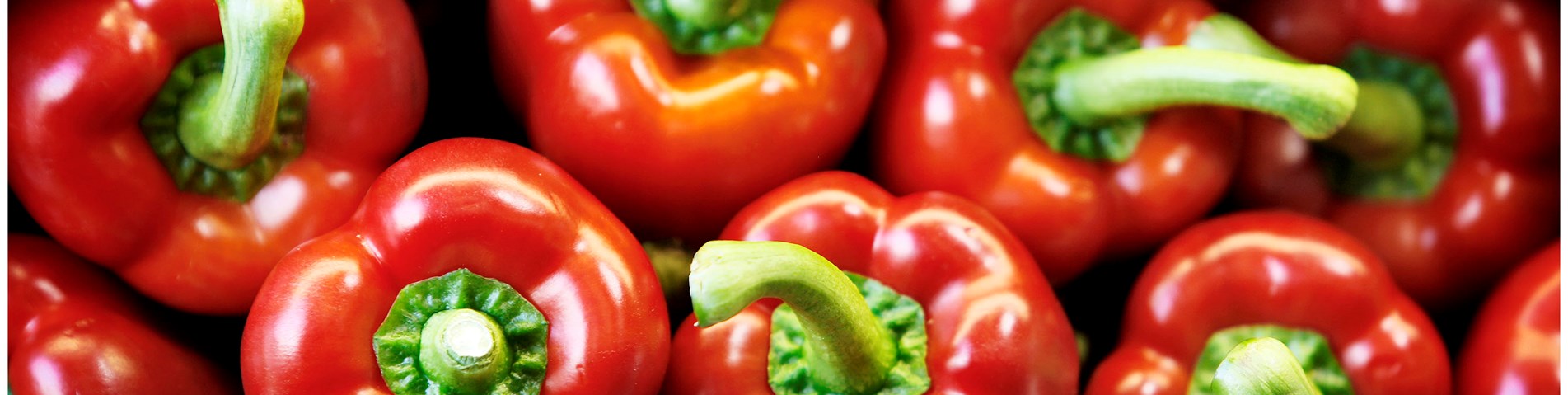
Inspection guidance
Inspection guidance
During the inspection there are certain records, documents and processes that the inspector will need to see.
The checklists below provide an overview of what will need to be available based on the activities you are certified to undertake. There is also guidance on completing the Action Summary Form (ASF) which details any issues identified at the inspection that require attention.
Read our standards for further information on what the inspection process entails.
-
Submit your forms on the Processor Portal
Use the certification portal to manage your organic certification, respond to audit actions and submit forms without having to keep track of emails.
Access the portal
-
Preparing for your first inspection
For applicants having their initial inspection.
Download
-
Wholesaler
Inspection guidance for handlers and traders of only pre-packaged retail & catering products (no processing, importing, packing or labelling).
Download
-
Storage
Inspection guidance for storage spaces of only pre-packaged retail & catering products (no processing, importing, packing or labelling).
Download
-
Abattoir
Inspection guidance for slaughterhouses, processors, importers, repacking, labelling of meat/poultry products.
Download
In this section...
Need further help?
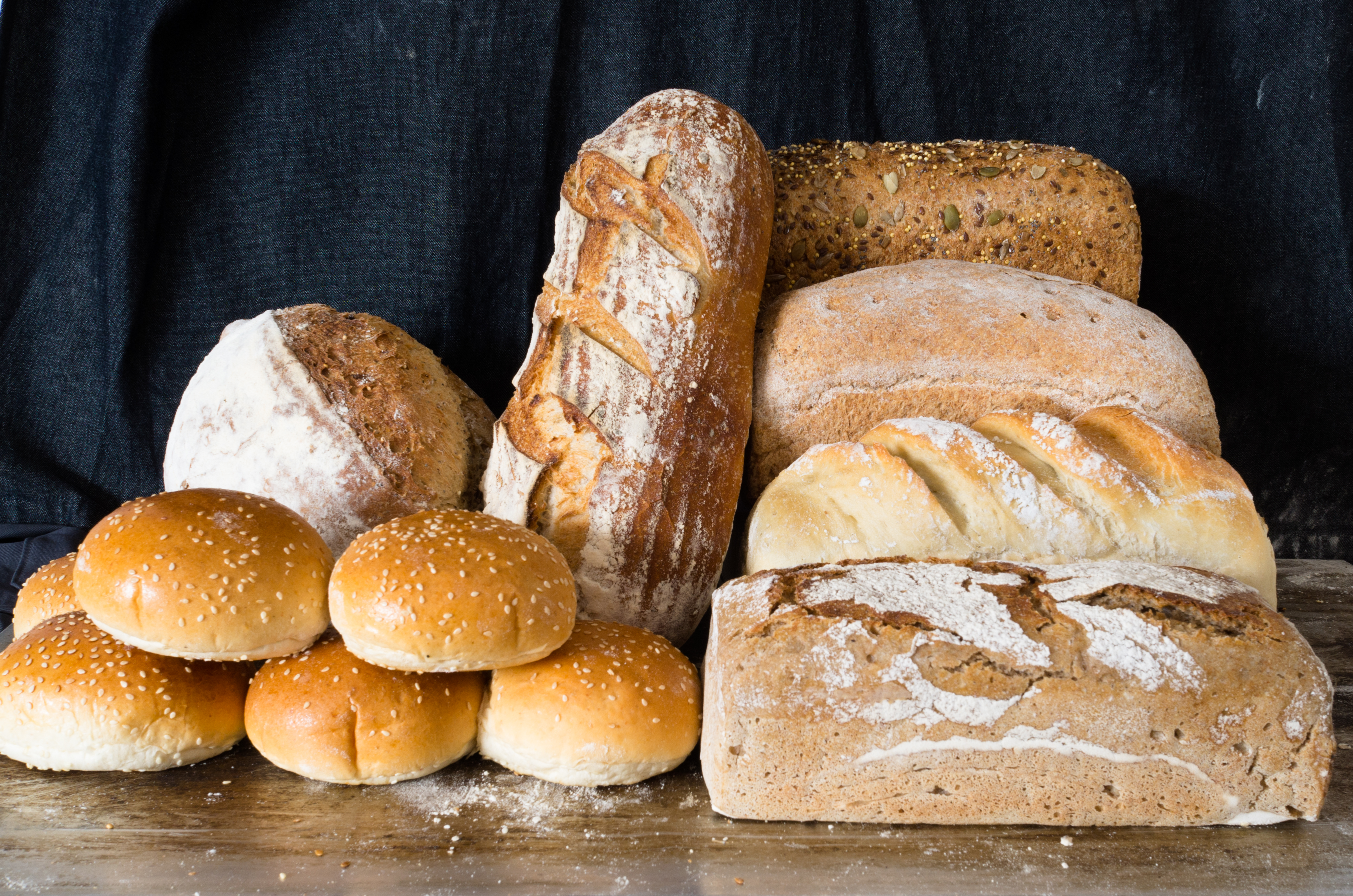